精密數(shù)控車銑復(fù)合機(jī)床是解決多工序加工工藝瓶頸的核心設(shè)備,其通過集成車削、銑削及其他輔助工藝,實(shí)現(xiàn)了復(fù)雜零件的高效、高精度加工。
一、傳統(tǒng)多工序加工的瓶頸
1.多次裝夾導(dǎo)致誤差累積
傳統(tǒng)加工需多次裝夾(如車削→銑削→鉆孔),每次裝夾可能引入定位誤差,影響零件精度。
示例:軸類零件在多次裝夾后,圓度誤差可能從±0.005mm增至±0.02mm。
2.效率低下
工序分散在不同設(shè)備(車床、銑床、鉆床等),需人工或物流周轉(zhuǎn),延長生產(chǎn)周期。
示例:加工一個復(fù)雜渦輪盤可能需要3天,其中裝夾和等待時間占40%。
3.成本高昂
多設(shè)備投入、人工操作及工裝夾具成本高,且廢品率較高(因誤差累積)。
復(fù)雜零件適應(yīng)性差
傳統(tǒng)工藝難以加工空間曲面、異形孔等特征,需依賴特殊工裝或手動操作。
1.一體化加工流程
一次裝夾完成多工序:
零件僅需一次裝夾,通過車削、銑削、鉆孔、攻絲、滾齒等復(fù)合工藝完成全部加工。
示例:加工齒輪軸時,車削外圓→銑削齒面→鉆孔→攻絲,全程無需拆裝。
多軸聯(lián)動與同步加工:
通過X/Z/B/C/Y軸聯(lián)動,實(shí)現(xiàn)復(fù)雜軌跡加工(如螺旋線、漸開線)。
示例:車削主軸時,同步銑削側(cè)面槽,縮短加工時間50%以上。
2.高精度保障
消除裝夾誤差:一次裝夾避免重復(fù)定位誤差,尺寸一致性顯著提升。
數(shù)據(jù):圓度誤差可控制在±0.002mm以內(nèi),圓柱度≤0.005mm。
熱變形補(bǔ)償:機(jī)床配備溫度傳感器和實(shí)時補(bǔ)償系統(tǒng),減少主軸和刀具熱變形對精度的影響。
在線檢測與反饋:集成激光測徑儀、接觸式測頭等,實(shí)時監(jiān)測工件尺寸并自動調(diào)整參數(shù)。
3.復(fù)雜工藝能力
空間曲面加工:通過B軸旋轉(zhuǎn)與多軸聯(lián)動,加工渦輪葉片、異形曲面等復(fù)雜幾何特征。
微結(jié)構(gòu)加工:支持細(xì)直徑刀具和高轉(zhuǎn)速主軸,實(shí)現(xiàn)微小孔、窄槽的精密加工。
復(fù)合工藝整合:
車削+銑削:如加工泵軸時,車削外圓同時銑削鍵槽。
車削+滾齒:一次性完成齒輪軸的外圓和齒面加工。
車削+鉆孔+攻絲:如汽車零部件的螺紋孔加工。
4.智能化與自動化
自適應(yīng)加工:根據(jù)材料硬度、刀具磨損狀態(tài)自動調(diào)整切削參數(shù)(如轉(zhuǎn)速、進(jìn)給量)。
機(jī)器人上下料:配合桁架機(jī)械手或關(guān)節(jié)機(jī)器人,實(shí)現(xiàn)無人化連續(xù)生產(chǎn)。
數(shù)字化管理:通過MES系統(tǒng)記錄加工參數(shù)、刀具壽命等數(shù)據(jù),支持追溯與優(yōu)化。
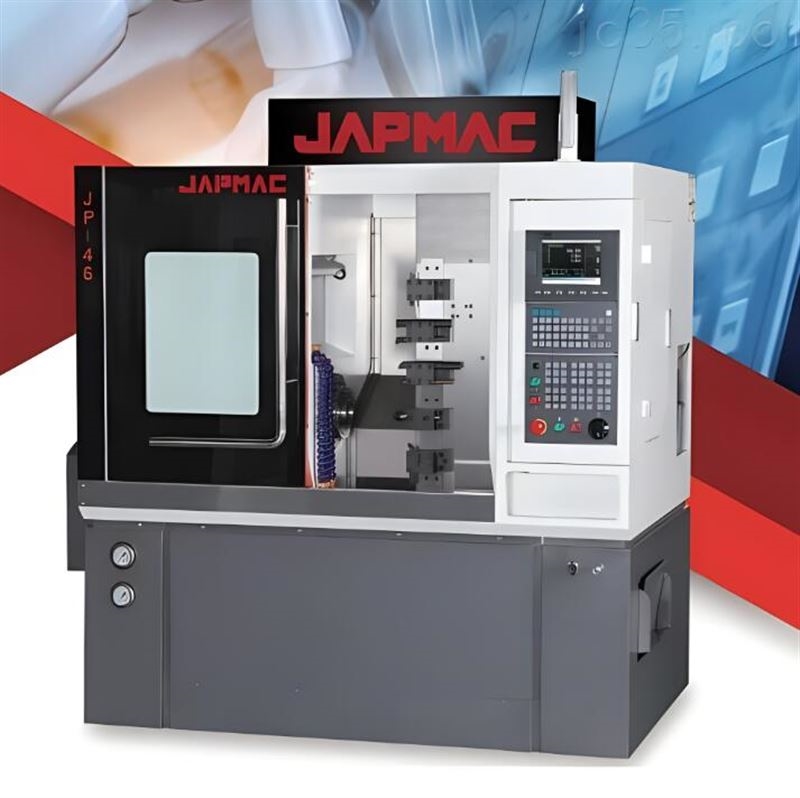